Products Details
Split Colloid Mill
We specialize in manufacturing colloid mills, so we understand your needs!
Stainless steel body, high material fineness, high production efficiency and small footprint
Colloid Mill is a second generation of wet ultra-particulate processing equipment
suitable to grind, homogenize, emulsify, disperse and mix various types of emulsion.
● Sanitary food-grade stainless steel. Except motor part, all contact parts are made of stainless steel, especially both dynamic grinding disc and static grinding disc are reinforced, making them better properties of corrosion-resistance and wear-resistance. In that case, the finished materials are non-pollution and safe.
● Colloid mill is an ideal equipment for processing fine materials with features of compact design, elegant appearance, good seal, stable performance, easy operation and high production efficiency.
● The motor and the base are separate in the split colloid mill, ensuring good stability, easy operation and a long service life of motor, furthermore it avoids material leakage to prevent motor from burning. It employs labyrinth seal, no wear, corrosion-resistance and less failure. Driving by pulley, it can change gear ratio, increase speed and make materials crushed finely.
● The vertical colloid mill solves the problem that small colloid mills couldn’t work continuously for a long time due to insufficient power and poor sealing. The motor is 220V, its advantages include compact overall structure, small size, light weight, reliable sealing structure and long hours of continuous work, especially suitable for small businesses and laboratory.
● How to know the capacity of a colloid mill ? The flow varies greatly according to materials of different density and viscosity. For example the flow of viscous paint and thin dairy fluids can be different more than 10 times on the same colloid mill.
● Capacity depends on concentration and viscosity of materials ? A colloid mill mainly consists of a motor, grinding parts, driving and base part. Among them, dynamic grinding core and static grinding core are key parts. So you may need to choose different models according to nature of materials.
● Various colloid mill are small vibration, work smoothly and no need foundation.
How to choose a suitable colloid mill?
Check model no.: The model no. of a colloid mill shows its structure type and diameter (mm) of grinding disc, which determines capacity.
Check capacity: the capacity of a colloid mill varies greatly according to materials of different density and viscosity.
Circulation Tube: suitable for low-viscosity materials that need recycling and reflux for grinding, such as soy milk, mung bean drinks, etc.
Rectangle Inlet: suitable for high and medium viscosity materials that don’t need reflux or grinding, such as peanut butter, chili sauce, etc.
Product Parameters
Note: (F split type / L vertical type / W horizontal type) Any change without prejudice to basic structure and performance is not informed in advance. Capacity varies according to nature of material and listed capacity is based on water as media. Additionally, JM-65 and JM-50 can also be equipped with 220V motor. Any other model with 3KW above motor is equipped with 380V motor.
Product Structure
Colloid mill is a processing machine of fine grinding and crushing fluid materials, mainly consist of motor, adjust unit, cooling unit, stator, rotor, shell, and etc, widely used in various industries.
1.Both rotor and stator are made of stainless steel, the rotor rotates at high speed and the stator keeps static, which makes materials passing the toothed bevel bear great force of shear and friction.
2.There is a pair of conical rotor and stator rotating at high speed inside a colloid mill. When materials pass the gap between the stator and rotor, they bear great force of shear, friction, centrifugal force and high-frequency vibration, finally making materials ground, emulsified, homogenized and dispersed.
3.It’s high efficiency of grinding ultra-fine particles by force of shear, grinding and high-speed stirring. And crush and grinding by relative movement of the disc tooth-shaped bevels.
4.Colloid Mill is an ideal wet-crushing equipment. Materials are ground, emulsified, crushed, mixed, dispersed and homogenized under forces of high-frequency vibration and high-speed vortex.
Working Principle
The basic work principle of colloid mill is that fluid or semi-fluid materials pass the gap between fixed tooth and rotation tooth which are relative high-speed interlocking to make materials bear strong shearing force, frictional force and high-frequency vibration force. Grinding is by the relative motion of toothed bevels, one rotates at high speed, the other keeps static. In that case, materials passing the toothed bevels are greatly sheared and rubbed. At the same time, those materials are under forces of high-frequency vibration and high-speed vortex, which make them ground, emulsified, crushed, mixed, dispersed and homogenized, finally fine finished products are achieved.
Rotation Disc and Static Disc High Shear
High Speed 2,900RPM to ensure the quality of grinding materials.
Product Showcase
Note: The standard hopper capacity is 4 - 12 liters, and the customized capacity is acceptable.
Conventional Type
Sanitary Type
Rectangle Outlet Type
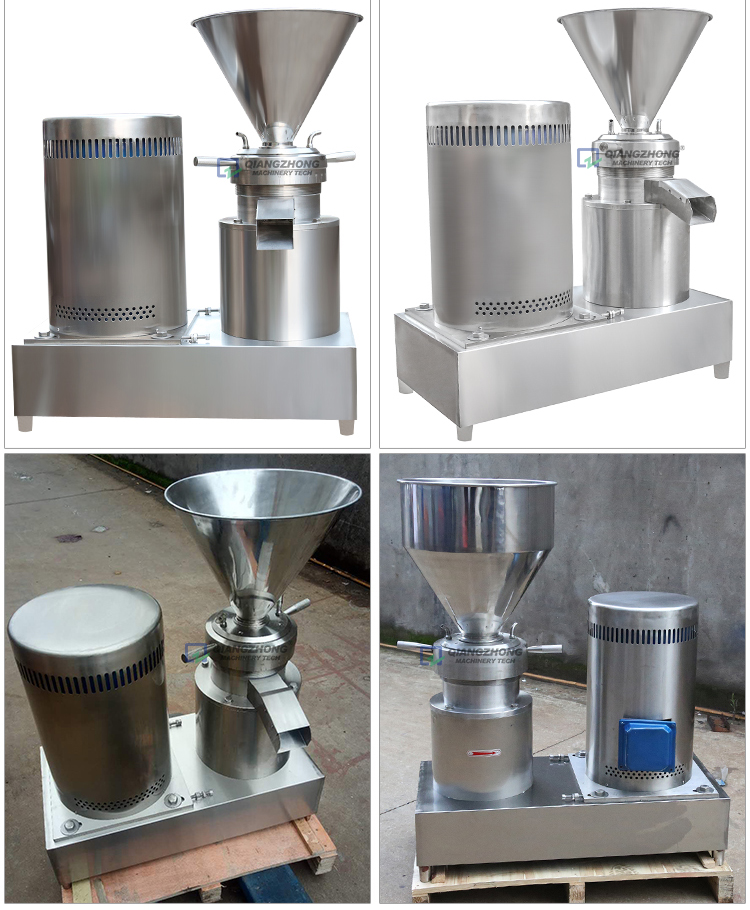
Application range
More about colloid mill
How to install a Colloid Mill :
● Please make sure the colloid mill is completely disinfected and cleaned before first usage.
● First, install hopper / feed pipe and discharge port / discharge circulation tube and then connect cooling pipe or drain pipe. Please do not block the discharge port to ensure materials discharge or cycle.
● Install power starter, ammeter and indicator. Turn on power and make the machine work, and then judge the direction of motor, the right direction should be clockwise when watching from the feed inlet.
● Adjust the grind disc gap. Loose handles, and then turn adjustment ring clockwise. With one hand deep into the rectangle port to rotate motor blades, and stop it immediately when there is friction on adjustment ring. Next, re-adjust the ring to make sure grind disc gap is larger than the aligned figure based on meeting the fineness of processing materials. This will ensure a longer life of grinding blade. Finally, turn the handle clockwise, lock the ring to make the grinding gap is fixed.
● Add cooling water, turn on the machine and put materials into operation immediately when the machine is on normal operation, please not allow the machine to idle for more than 15 seconds.
● Pay attention to motor loading, please reduce feeding materials if it is overloaded.
● Since colloid mill is a high-precision machine, working at high speed, grinding gap is minimal, any operator should strictly operate the machine according to the operation rule. If there is any fault, please immediately stop operation and shut down the machine, only re-operate the machine once troubleshooting is completed.
● Do remember to clean the colloid mill thoroughly every time after use to prevent any remains that may lead to mechanical seal adhesion and leakage.
Why does the grinding head loose ?
Correct rotation direction of grinding head is counterclockwise (an arrow illustrates on the
machine). If the grinding head works reverses (clockwise), cutter head and materials will collide with each other, leading to threads loosen in the reverse direction. As service time increases, the thread of the cutter head will fall off. While if grinding head rotates counterclockwise (the correct direction of rotation), the thread will be tighter and tighter with conflict of materials, the cutter won’t drop. It is suggested that if colloid works reverse when you turn on the machine, please immediately shut it down because if working reversal for long time, the cutter will loose.
Precautions:
Please make sure that quartz, broken glass, metal and other hard objects are not mixed in processing materials, better filter the materials in advance, avoiding any damage to rotation disc and static disc.
Right way to adjust the gap between the grinding discs:
loose handles counterclockwise, and then turn adjustment ring clockwise. With one hand deep into the rectangle port to rotate motor blades, and stop it immediately when there is friction on adjustment ring. Next, re-adjust the ring to make sure grind disc gap is larger than the aligned figure based on meeting the fineness of processing materials. This will ensure a longer life of grinding blade. Finally, turn the handle clockwise, lock the ring to make the grinding gap is fixed.
Disassembly Instructions:
1.Remove hopper counterclockwise, then rotate disc handle counterclockwise, release static disc
2.Pull up the static disc
3.Disassemble V-shape feeding blade counterclockwise.
4. With a screw to pull out of rotation disc, disassembly is completed.
Please note: assembly steps are on the contrary.
Micro Filter Housing,
Indian Pressure Cooker,
Beef Cooker,
Emulsification Mixing Tank,
Diaphragm Pneumatic Pump,
Brewing All In One,
Mineral Grinder,
Small Industrial Grinder,
Milk Strainer,
Vegetable Ghee Production Line,