Model No | Motor Power(kw) | Filter Pressure Filter Size Filtration Water Filtration Layers of Dimensions | ||||||
(Mpa) | (mm) | Area(nf) Flow(t/h) Medium(um) Plates | (L*W-H) | |||||
WBG-100 | 0.55 | 0.15 | 100 | 0.078 | 0.8 | 0.8 | 10 | 680x310x580 |
WBG-150 | 0.75 | 0/15 | 150 | 0.17 | 0.15 | 0.8 | 10 | 780x350x700 |
WBG-200 | 1.1 | 0.15 | 200 | 0.34 | 2 | 0.8 | 10 | 820x380x760 |
WBG-300 | 1.1 | 0.15 | 300 | 0.7 | 4 | 0.8 | 10 | 920x500x900 |
WBG-400 | 1.1 | 0.15 | 400 | 1.25 | 6 | 0.8 | 10 | 1260x600x1120 |
WBG-400 | 1.5 | 0.15 | 400 | 2 | 9 | 0.8 | 16 | 1350x600x1150 |
WBG-400 | 1.5 | 0.2 | 400 | 2.5 | 10 | 0.8 | 20 | 1420x600x1180 |
WBG-400 | 22 | 0.3 | 400 | 4 | 13 | 0.8 | 32 | 1588x600x1180 |
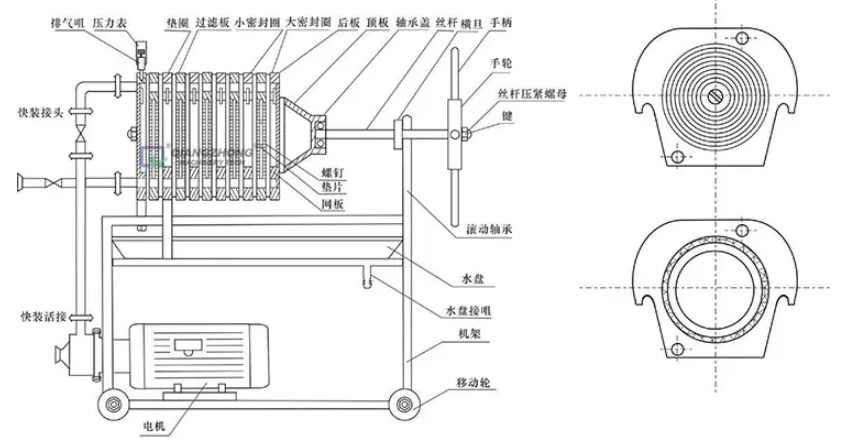
PRODUCT STRUCTURE
Except the motor, the other parts of the machine are made of 304 or 316L high-quality corrosion- resistant stainless steel, suitable for filtering all kinds of PH value of the acid-base solution. The machine adopts pressurized airtight filtration,low filter loss, good filtration quality and high efficiency. The filter section is composed of ten filter plates, with a large filtration area and a large circulation volume. According to the production process requirements (preliminary care, decarbonization, particulate removal, semi-fine filtration, fine filtration) of the solution to be filtered, different filter membranes can be replaced, and the number of filter plate layers can be appropriately reduced or increased according to production flow requirements to meet the production needs. Therefore, this machine is a multi-use machine with a wide range of features. The filter plate adopts a plane thread mesh structure, which is an advanced structure, no deformation, easy cleaning, and it can effectively prolong the service life of various filter membranes and save the production cost. This machine is equipped with stainless steel infusion pump with a small power motor of power consumption. Rubber wheels are installed under the base for mobile use, flexible movement and easy operation.
- When installing or replacing the filter materiaL it should be tightly attached to the silicone rubber ring, the position must be moderately flat, and then press the moving plate to prevent leakage.
- If you want to stop the equipment. please first close the inlet ball valve, and then cut off the power to prevent the liquid back against the impact and destroy the filter membrane.
I | Pump couldn't switch on or overload at startup | 1. motor or power failure 2. pump stuck 3. discharge valve is not closed | 1. check the motor or power supply 2. inspection pump casing, impeller 3. close and restart the discharge valve |
II | Pump does not discharge | 1.insufficient liquid or gas not drained in airbag 2.wrong direction of motor rotation 3.the speed is too low 4. the suction height is too high | 1. refill the pump 2. check and correct direction of rotation 3. check and adjust speed 4. reduce the suction height |
III | Pump discharge interruption | 1. suction pipe leakage 2. gas not drained in airbag 3. inhalation is blocked by foreign matter 4. a lot of inhaled gas | 1. check and repair suction connection and the sealing 2. refill the pump 3. stop the pump and remove foreign materials 4. check whether there is vortex at the inlet and whether flooding depth is too shallow. etc. |
IV | Insufficient Flow | 1. same with (II). (Ill) 2. the system static lift increase 3. increased resistance loss 4. pump impeller blockage 5. leakage | 1. take corresponding measures
3. inspect pipeline and the check valve 4. cleaning and exchange impeller
|
V | Insufficient Lift | 1. same with (II). (Ill) 1JIV)4
3. too much flow | 1. take corresponding measures 2. check the nature of related materials 3. reduce the flow |
VI | Noisy | 1. the impeller and the pump casing friction 2. same with (V) 3 3. increase of liquid unit weight 4. the pump shaft bending | 1. inspect and replace the faulty parts 2. take corresponding measures 3. check unit weight 4. replace the pump shaft |
VII | Equipment vibration | 1. samer with the (III) 4 2. surging 3. impeller damage | 1. take corresponding measures 2. check the discharge of liquid and pressure levels 3. inspect and replace the impeller |